プラスチック射出成形(インジェクション)とは?仕組みや流れ等の基礎知識
射出成形の仕組み
射出成形(別名:インジェクション)とは、加熱溶融した可塑性(かそせい:粘土のような性質のこと)樹脂材料を、高圧で金型内に射出(注入)し、冷却固化させた後、製品を取り出す手法・方法のことです。
その工程が注射器で液体を送り込む様子に似ていることから、「射出成形」と呼ばれています。
射出成形の特徴は、液状になったプラスチックを金型に流し込む成形手法から、複雑な形状の製品でも素早く大量に連続して製造することが出来る点にあります。一般的にはロットが大きく大量生産するような製品の製造に向いており、沢山のプラスチック製品を短時間に大量に製造する事を得意としています。
射出成形を行うためには、射出成形機という成形用の機械を使用します。
射出成形機はその大きさ(トン数)によって作れる製品の大きさが決まります。
通常トン数が大きな射出成形機ほど大きな製品が製造でき、小さな射出成形機ほど小さな製品しか作れなくなります。 フジデノロモールドでは九州でも数少ない超大型の射出成形機(1000t)を揃えているため、自動車のバンパーなどの大きな製品にも対応可能です。
射出成形を用いて製品ができるまで
プラスチックの材料(樹脂)は熱を加えると、ドロドロに溶融して加工しやすい液状になります。
それらを金型に流し込んでから、時間をかけて再び冷却すると金型に合わせて固まり、製品が出来上がります。 一般的な射出成形の流れをご紹介します。
①金型を製作する
まず製品を作るための金型を製作します。 金型は製品のサイズと個数によってその大きさと金額が変わります。一般的に大きな金型ほど価格も高くなる傾向にありますが、一度に製造できる個数が1個なのか100個なのかで、大きく生産コストが変わるため、最終的な生産数を見越してどの程度の金型が必要か考える必要があります。
②材料を選択する
通常は、製品の設計時点で適切な耐性や物性をもつ材料は決まっているので、それに合わせた材料を準備します。
③材料と金型をセットして製造開始
材料と金型に合わせて、射出成形機の温度と時間を設定し、製造を開始します。
射出成形機の製造工程
1.元のプラスチック材料は米粒状になっており、それらを加熱筒シリンダーへ送り込みます。
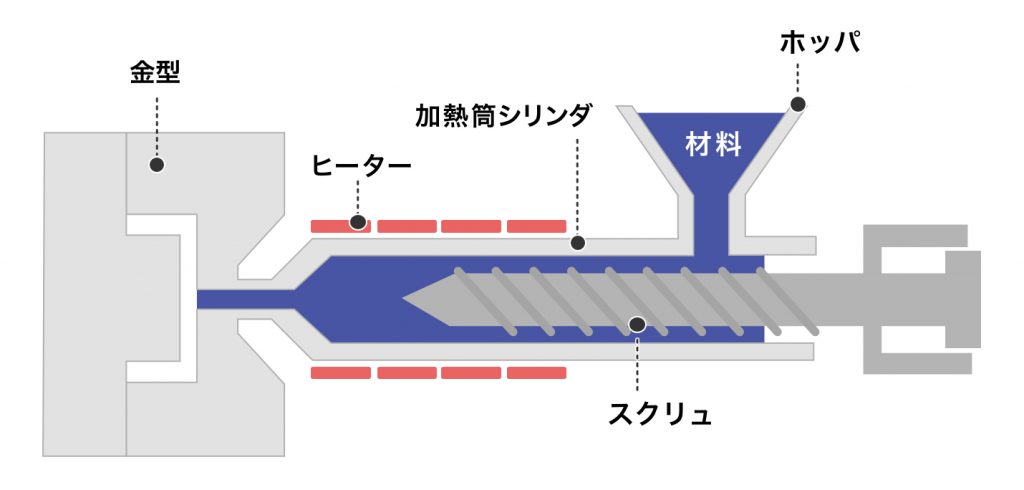
2.シリンダーに送られた材料は、ヒーターによって高熱で溶かされながら、スクリューで前へと押し流されて行きます。
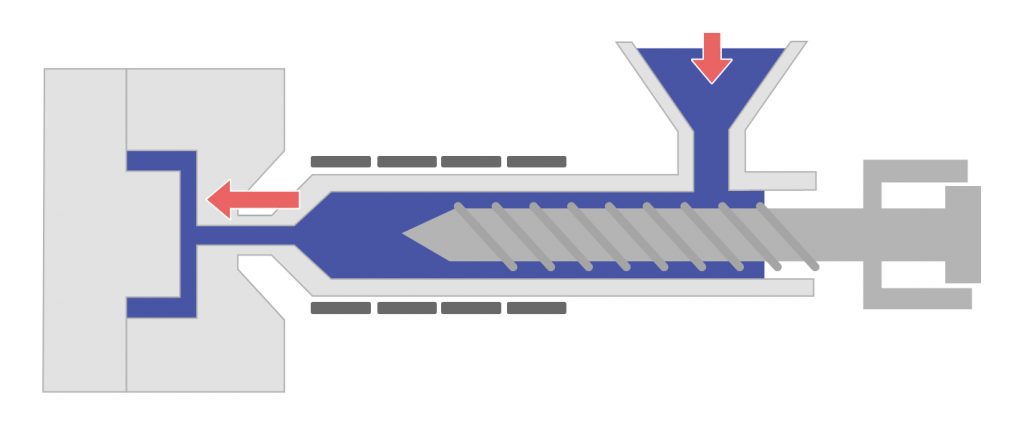
3.金型に設置された挿入口からプラスチック材料を注射器のように射出し、金型を材料で満たします。金型内に流し込まれたプラスチックは冷えて固まるまで数秒〜数分間圧力をかけた状態で冷却します。
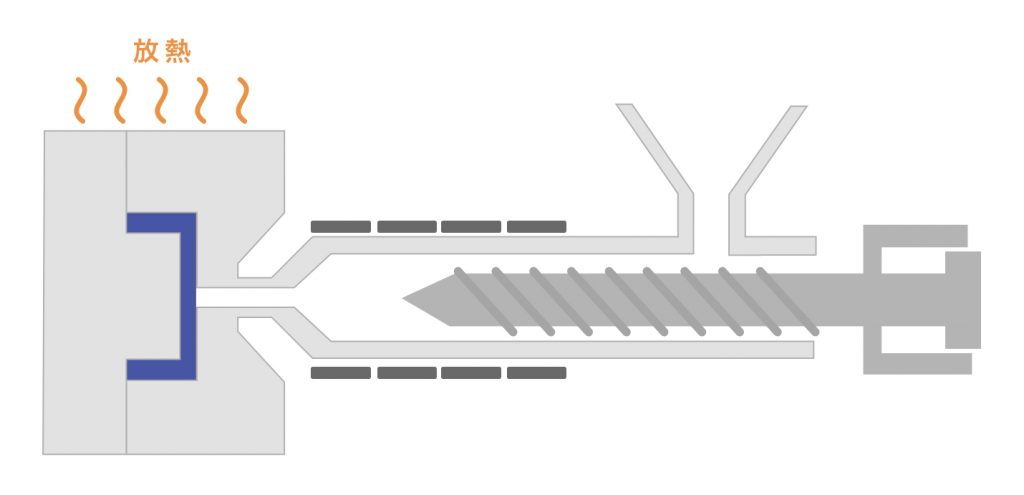
4.製品が固まったら、金型を開いて成形品を取り出します。
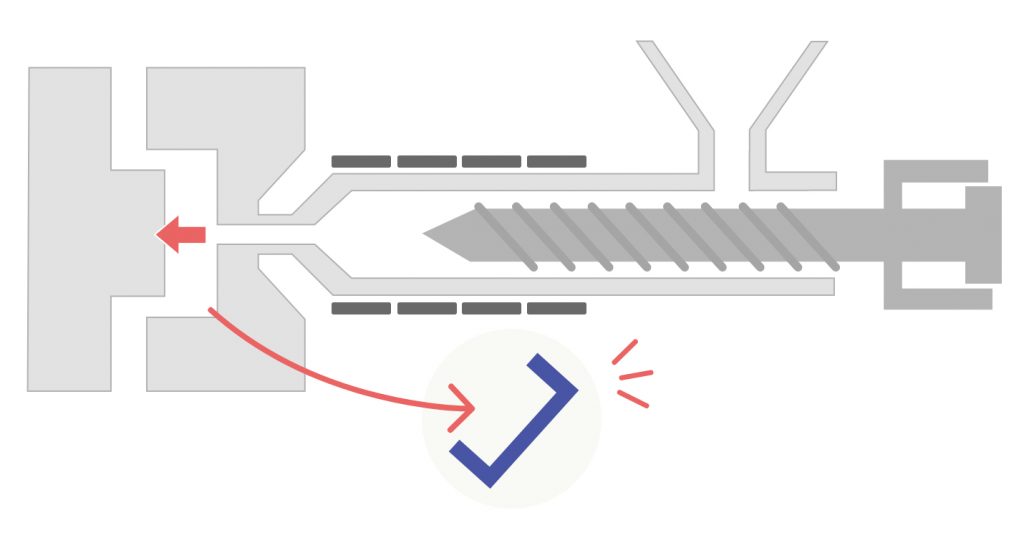
④仕上げ・検品
射出成形機から製品が出てきた時点では、バリと呼ばれる余分な部分を取り除いたり、他の部品と組み立てたりする必要があります。
最後は人の手で仕上げられ、市場に出せる状態になるのです。
そして最終的には目視で検品していき、不良品や規格外品はこの時点で徹底的に弾かれ、配送センターへ送られます。
⑤配送
完成した製品がロットごとに小分けにされ、配送センターから納品先へ発送されます。
フジデノロモールドには社内に配送部があり、大型トラックを多数所有しているので配送圏内であればそのままお客様の元へ直送されます。
射出成形機の種類と製造できる製品
射出成形機にはその大きさ(型締力)に応じて、製造できる製品が異なります。
基本的には大きな射出成形機ほど、大きな製品を製造でき、一度に大量の製品を製造することが可能です。
これは大きな製品・大量の製品を製造するためには、それだけ金型のサイズが大きくなるためで、金型を設置できる射出成形機も限られてくるからです。
逆に小さな製品になると、大型の射出成形機では製造コストが高くなってしまうため、小さな射出成形機の方が向いています。
製造する製品の大きさと製造するロットに合わせた射出成形機が必要なのです。
射出成形機のサイズは型締力(かたじめりょく)といって、型に掛けられる圧力の大きさをt(トン)で表すのが一般的です。
小型の成形機の型締力は50t程ですが、超大型の成形機になると1000tの型締力を持っており、そのサイズも大型トラックほどの大きさになります。
フジデノロモールドで実際に使われている射出成形機
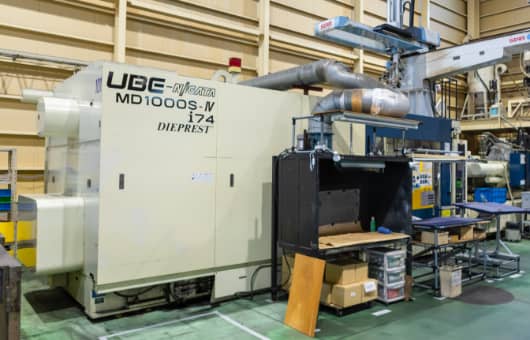
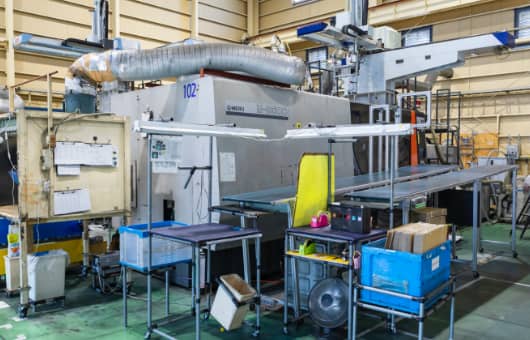
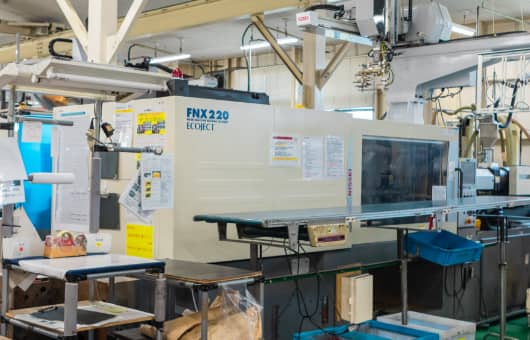
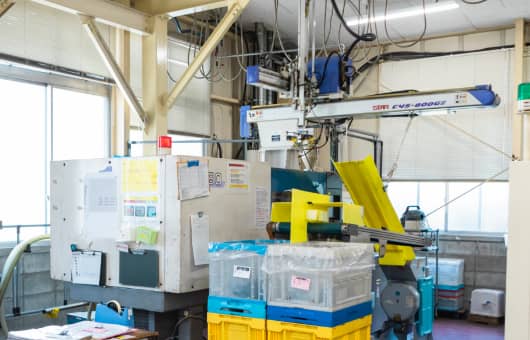
フジデノロモールドでは、小型は50tから大型は1000tまで10種類以上の射出成形機を保有しているので、ありとあらゆるサイズ・ロットの製品に対応しております。
九州(福岡)でプラスチック射出成形の製造会社をお探しの場合は、ご用途やご予算に応じ、ご提案させていただきますので、ぜひ一度フジデノロモールドへご相談ください。